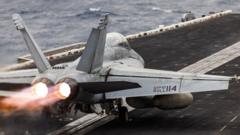
Coatings: The Unsung Heroes of Engineering Performance
Coatings are transformative technologies that dramatically enhance the functionality and durability of materials across various industries, from aerospace to manufacturing. These thin layers can enable machines to operate in extreme conditions and significantly improve performance.
In jet engine technology, coatings are crucial for overcoming seemingly impossible engineering challenges. Jet engines generate temperatures exceeding 1,000°C, which would normally melt the underlying metal components. Heat-resistant ceramic coatings solve this problem, allowing engines to operate efficiently. Researchers are continually developing stronger coatings that enable engines to run hotter, potentially reducing fuel consumption by up to 8% with just a 30°C temperature increase.
Beyond aerospace, coatings have diverse applications. For instance, researchers at MIT have developed specialized coatings to address challenges in space exploration. One innovative coating prevents biofilm formation in low-gravity environments, which can cause mechanical failures in spacecraft fluid systems. The coating works by creating an extremely slippery surface that prevents bacterial accumulation.
In industrial manufacturing, coatings provide remarkable benefits. A silicon carbide-based coating developed by researchers at the Norwegian University of Science and Technology has revolutionized aluminum manufacturing. This “non-stick” coating prevents molten aluminum from adhering to expensive equipment, extending tool life and reducing maintenance costs. One US machinery company reported reducing annual tool rebuild expenses from $4.5 million to $1.3 million by using such a coating.
However, coating technology is not without challenges. Experts like Andy Hopkinson from Safinah Group highlight that coatings don’t always perform as expected. Issues can range from fire-resistant paint peeling off car park structures to ineffective anti-fouling coatings on ship hulls that fail to prevent marine organism attachment.
The complexity of coating selection is significant. Factors like environmental conditions, intended use, and specific performance requirements must be carefully considered. While coatings typically represent only 1-2% of a project’s cost, failures can lead to exponential expenses.
Despite these challenges, researchers remain optimistic about coating technology’s future. They continue exploring innovative solutions that could dramatically improve machine performance, infrastructure durability, and operational efficiency across multiple sectors.
The potential of coatings extends from practical industrial applications to seemingly mundane everyday uses. Professor Varanasi, who developed slippery coatings, has even commercialized technology allowing consumers to extract every last bit of toothpaste from tubes.
As research progresses, coatings represent a fascinating intersection of materials science, engineering, and innovation – quietly revolutionizing how we design and use technology in increasingly demanding environments.